Project description
As wind energy plays a very important role in the energy transition, it is crucial to build wind turbines more sustainably and use resources more efficiently. The system described in this project is meant to contribute to this.
The aim of the project is to develop an integral rotor blade design to implement a hydropneumatic flywheel accumulator. In the process, we aim to partially replace load-bearing structures of the rotor blade (webs and chords) by the components of the flywheel accumulator. This requires a complete redesign of the rotor blade and an evaluation of the mechanical loads in the entire wind turbine. The operation of the flywheel system significantly reduces the fatigue loads and some extreme loads on the most important components of the wind turbine, such as the foundation, tower and rotor blades.
The aim of the first project phase is to expand existing load simulation software in order to be able to simulate variable structural properties of the blade. Initially, we aim to use a rotor blade with a flywheel accumulator as an integral structural element.
In a subsequent second phase, the effects of the integral rotor blade design on the mechanical loads in the entire wind turbine will be reassessed. This project phase will focus on the wind turbine simulation with variable mass properties of the blades. Control functionalities will be developed that allow the flywheel accumulator to specifically reduce the mechanical loads of the individual design load cases (DLC). Based on these simulations, the other components of the wind turbine are iteratively adapted to the prevailing loads.
The combination of the load-minimising control functionalities of the flywheel storage system and the redesign of the rotor blade with the storage components as stiffening components will mean that the rotor blades, the tower, the foundation and possibly the drive train of the wind turbine can be dimensioned lighter. This will reduce the amount of material required to manufacture these components. This reducing of the material input saves resources and reduces energy consumption compared to the current manufacturing process for wind turbines. Less material being used in the production of components also leads to lower costs when wind turbines have to be dismantled and recycled. The CO2 footprint is reduced and the wind turbine becomes more sustainable.
Based on previous research at the Wind Energy Technology Institute (WETI) and the development work at HYDAC Technology, the integral design of a wind turbine with a flywheel accumulator is to be implemented in an industrial research project by the renowned wind turbine developer AEROVIDE GmbH. To this end, the flexible carbon fiber reinforced plastic (CFRP) piston accumulators developed at HYDAC must be scaled up for use as structural components in rotor blades at WETI. At AEROVIDE GmbH, these CFRP components are used in rotor blade design.
Funding
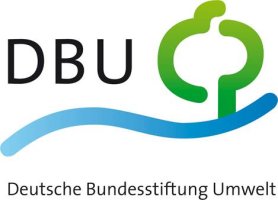